Gmaw(MIG/MAG)Welding Machine
220V 200A 5 kg wire synergic processional aluminum MIG welding machine
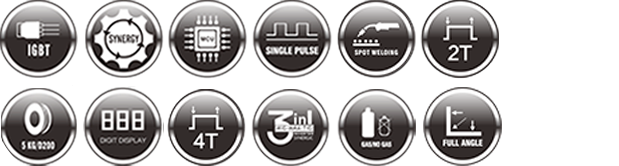
What do we do
Based in Wenling City, PONEY has established as leading China 220V 200A 5 kg wire synergic processional aluminum MIG welding machine suppliers and OEM/ODM 220V 200A 5 kg wire synergic processional aluminum MIG welding machine company engaging in the production of welding machine, cutting machine and car battery charger.
How well we did it
Our technicians are dedicated to developing groundbreaking products, and equipped with the latest production processes, we can guarantee my products are of high and consistent quality. Unique and modernly designed products make our company a reliable partner for industry and trade. We are active in the international welding market, pursue excellent quality, and provide our customers with efficient solutions to create greater value.
Our product quality
In PONEY, each 220V 200A 5 kg wire synergic processional aluminum MIG welding machine goes through stringent testings and inspections that always guarantees superior quality, reliability and safety which acknowledged by clients from across the world. Supported by sound management and expertise of technology, PONEY products are accredited with certifications like CE GS, ISO, ROHS, and others.
Enterprise establishment
Product Varieties
Welder Series
Production capacity
The versatility of the Digital Control ARC Welding Machine is a testament to its advanced technology, which allows for good performance across a range of welding positions. These machines are designed to handle vertical, horizontal, and other complex welding positions with precision and efficiency, setting them apart from traditional welding equipment. The question of how Digital Control ARC Welding Machines perform in different welding positions highlights their adaptability and the benefits they offer in modern welding applications.
The ability of Digital Control ARC Welding Machines to maintain consistent performance in various orientations is a direct result of their sophisticated control systems. These systems are capable of adjusting the welding parameters in real time, ensuring that the arc is stable and the weld pool is controlled, regardless of the position. This is particularly important in vertical and overhead welding, where gravity can cause the weld pool to sag, causing poor weld quality. The digital control systems of these Digital Control ARC Welding Machines can compensate for such factors, maintaining a consistent arc length and reducing the risk of weld defects.
In horizontal welding positions, Digital Control ARC Welding Machines excel by providing a stable and controlled welding environment. The machines can adjust the amperage and voltage to maintain a consistent arc, even as the welder moves along the joint. This results in a more uniform weld bead and fewer instances of undercutting or burn-through, which are common issues with traditional welding equipment. The precision of the digital controls also allows for better control over the heat input, which is crucial for avoiding distortion in the workpiece.
When it comes to vertical welding, Digital Control ARC Welding Machines demonstrate their adaptability by maintaining a stable arc even as the welder moves upward. The digital control system can adjust the welding parameters to counteract the effects of gravity, ensuring that the weld pool remains stable and the weld bead is uniform. This is a significant improvement over traditional welding methods, which often struggle with maintaining a consistent arc in vertical positions, causing a higher incidence of spatter and weld defects.
Overhead welding is another position where Digital Control ARC Welding Machines shine. The ability to control the welding parameters with precision allows these Digital Control ARC Welding Machines to maintain a stable arc even in challenging positions. The digital control system can adjust the amperage and voltage to ensure that the weld pool remains stable, reducing the risk of weld defects such as porosity and lack of fusion. This is particularly important in overhead welding, where the welder has limited visibility and control over the weld pool.
The adaptability of Digital Control ARC Welding Machines is further enhanced by their ability to store and recall welding parameters for different welding positions. This feature allows welders to quickly switch between positions without having to manually adjust the welding parameters, saving time and ensuring consistency in the welding process. The digital control system can also monitor the welding process in real time, providing feedback on the quality of the weld and alerting the welder to any issues that may arise.
In conclusion, the performance of Digital Control ARC Welding Machines in various welding positions is a testament to their advanced technology and digital control systems. These Digital Control ARC Welding Machines offer a significant advantage over traditional welding equipment, providing consistent performance, improved weld quality, and greater adaptability in a range of welding positions. The integration of digital controls into ARC welding machines has changed the industry, offering welders a tool that can handle the complexities of modern welding with ease and precision.
In the welding industry, the reduction of spatter is a critical factor that directly impacts the quality of the weld, the efficiency of the process, and the safety of the work environment. Digital Control ARC Welding Machine has emerged as a causing solution in addressing this issue, offering advanced control mechanisms that significantly minimize spatter during the welding process. The integration of digital technology into welding equipment has changed the way spatter is managed, causing cleaner, more efficient, and safer welding operations.
One of the primary ways in which Digital Control ARC Welding Machines reduce spatter is through precise control over the welding parameters. Traditional welding machines often rely on manual adjustments, which can cause inconsistencies and, consequently, increased spatter. In contrast, Digital Control ARC Welding Machines allow for the fine-tuning of parameters such as voltage, current, and wire feed speed, ensuring a more consistent and controlled welding arc. This precision helps to decrease the formation of the spatter, as the arc is more stable and less likely to produce the erratic movements that can cause the spatter.
Another advantage of Digital Control ARC Welding Machines in reducing spatter is their ability to maintain a stable arc length. The digital control system continuously monitors and adjusts the arc length, preventing it from becoming too long or too short. An unstable arc length can cause the arc to push the molten metal away from the weld pool, causing a spatter. By maintaining a consistent arc length, Digital Control ARC Welding Machines ensure that the molten metal is directed into the weld pool, reducing the likelihood of spatter formation.
The use of advanced software in Digital Control ARC Welding Machines also plays a crucial role in minimizing spatter. These machines often come equipped with software that can predict and compensate for changes in the welding environment, such as variations in wire feed speed or voltage fluctuations. This predictive capability allows the machine to adjust its parameters in real-time, ensuring suitable welding conditions and further reducing the potential for spatter.
In addition to the technical advantages, Digital Control ARC Welding Machines also offer user-friendly interfaces that make it easier for operators to set and adjust parameters. This ease of use can cause more consistent welding practices, as operators can more accurately input the desired settings and make adjustments as needed. The reduction in user error contributes to a decrease in spatter, as the welding process is less likely to be disrupted by incorrect settings or operator mistakes.
Furthermore, Digital Control ARC Welding Machines often feature advanced cooling systems that help to manage the heat generated during the welding process. By effectively dissipating heat, these systems reduce the thermal stress on the welding components, which can contribute to the spatter. The controlled thermal environment also helps to maintain a more stable arc, further reducing the likelihood of spatter.
In conclusion, Digital Control ARC Welding Machines have proven to be highly effective in reducing spatter during the welding process. Their advanced digital controls, precise parameter adjustments, stable arc length maintenance, predictive software capabilities, user-friendly interfaces, and effective cooling systems all contribute to a significant reduction in spatter. As the welding industry continues to evolve, the adoption of Digital Control ARC Welding Machines will play a crucial role in improving the quality, efficiency, and safety of welding operations worldwide.